스마트 과제 1038건 수행, 수율 끌어 올리고 인건비 1630억 이익
원가 계산·분석 기존 인력 자원으로 8일 소요···AI 시스템은 '3분'
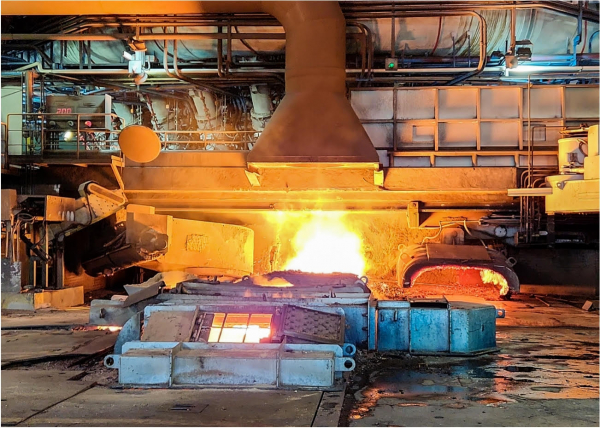
[시사저널e=유호승 기자] 포스코가 인공지능(AI)과 빅데이터 등을 기반으로 스마트팩토리 전환에 속도를 내고 있다. 인력이 아닌 자동화 시스템을 통해 철강 제품 생산 과정에서 나타날 수 있는 산업재해를 ‘제로(0)’로 만들겠다는 목표를 달성하기 위해서다.
포스코는 2016년부터 스마트팩토리 전환에 집중했다. 초기에는 철강 제품 라인 별로 작은 공정부터 추진하던 자동화 공정은 현재 생산 계획부터 출하까지 전 공정으로 범위가 크게 늘어났다.
천시열 포스코 포항제철소 공정품질담당 부소장은 “현재까지 1000건 이상의 스마트 기술 과제를 수행했다”며 “이 과정에서 완수한 대표적인 수행 과제는 과거에는 작업자의 조이스틱 운용 능력에 따라 생산성이나 품질에 편차가 있었지만 AI를 통한 자동화 시스템으로 대체된 후에는 작업 속도도 빨라지고 안정적 품질의 제품이 만들어지고 있다”고 말했다.
포스코에 따르면 스마트팩토리 전환에 나선 후 올해 3월까지 실행한 스마트과제는 총 1038건이다. 이 과정에서 자동화를 통해 높아진 수율(완성품 중 합격 제품 비율)과 줄어든 인건비는 1630억원 규모다.
이같은 성과로 포스코는 2019년 7월 국내 최초로 세계경제포럼(WEF)이 선정하는 ‘등대공장’으로 선정됐다. 등대공장은 밤하늘에 등대가 길을 안내하는 것처럼 AI와 빅데이터, 사물인터넷(IoT) 등 4차 산업혁명 핵심 기술을 적극 도입해 제조업의 미래를 이끄는 기업에 주어지는 호칭이다.
2022년 기준 전세계 등대공장 145곳 중 철강사는 포스코를 포함해 인도 타타스틸(인도 2곳·네덜란드 1곳)과 중국 보산철강 등 5곳뿐이다.
스마트팩토리화에 나선지 8년이 지난 현재 포스코는 제선·제강·연주 등 전 공정 자동화까지 많은 시간이 걸리지 않을 것으로 자신감을 내비쳤다.
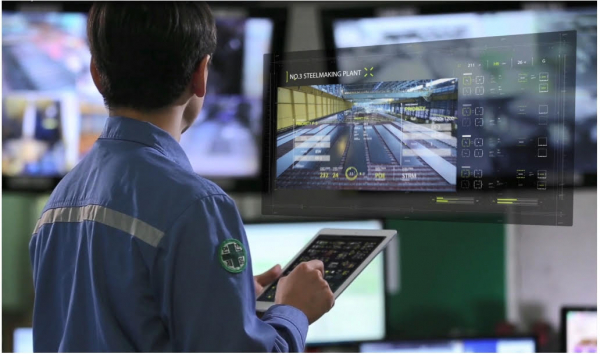
먼저 고로에 철광석·코크스·석회석을 넣고 열을 가해 선철(용광로에서 철광석을 녹여 만든, 탄소가 다량 함유된 철)을 만드는 제선 공정은 AI가 데이터를 학습해 예측·관리하는 스마트 고로로 변화했다.
선철에 포함된 불순물을 제거하고 철의 함유량을 적절히 조정하는 과정인 제강과 쇳물을 슬라브 등으로 생산하는 연주 공정 등에선 온도·성분을 제어하는 AI 통합 제어 시스템으로 중단이나 지연 없는 연속 작업이 가능해졌다.
또한 도금 과정에선 제품의 종류나 두께, 폭, 조업 조건 등에 따라 목표 도금량을 자동화돼 제어하고 있다. 스마트 고로와 도금 기술 등은 국가핵심기술로 등재되기도 했다.
포스코는 “조업 과정에서 발생하는 원가 계산과 분석 등에도 AI가 적용 활용되고 있다”며 “원자재값을 줄일 수 있도록 적정 수준의 원료 투입량, 최적 배합 등을 시스템이 처리하면서 기존에 8일 걸리던 작업기간을 3분으로 단축했다”고 밝혔다.
포스코뿐만 아니라 현대제철 등 다른 철강 기업도 스마트팩토리화에 분주한 모습이다. 현대제철은 ‘4족 보행로봇(SPOT)’을 활용해 산소가스 밸브 개폐 및 위험 지역에 대한 일상 점검 등을 실시하고 있다. 비상 상황이 발생할 경우에는 이 로봇을 투입해 화재·폭발 등 2차 재해를 예방해 작업자의 안전을 도모한다.
철강업계 관계자는 “제철소의 스마트팩토리화는 생산 공정의 신속·정확성과 함께 근로자의 안전성도 높일 수 있는 프로세스”라며 “안전을 최우선 과제로 인식하고 최신 기술을 현장에 더욱 빠르게 접목시킬 수 있도록 기업별로 다양한 시도를 하고 있다”고 전했다.